Having issues achieving a consistent color with the application of black oxide? Start by looking at your pretreatment. Connor Callais of Hubbard-Hall offers advice for troubleshooting your black oxide process. #asktheexpert
Q: We’ve been running into issues with achieving a consistent color with our black oxide application, often becoming splotchy or occasionally having a reddish cast over the black finish. What would be the best way to troubleshoot our operation so that we can regain our product’s uniform coloring? Wood Plyo Box
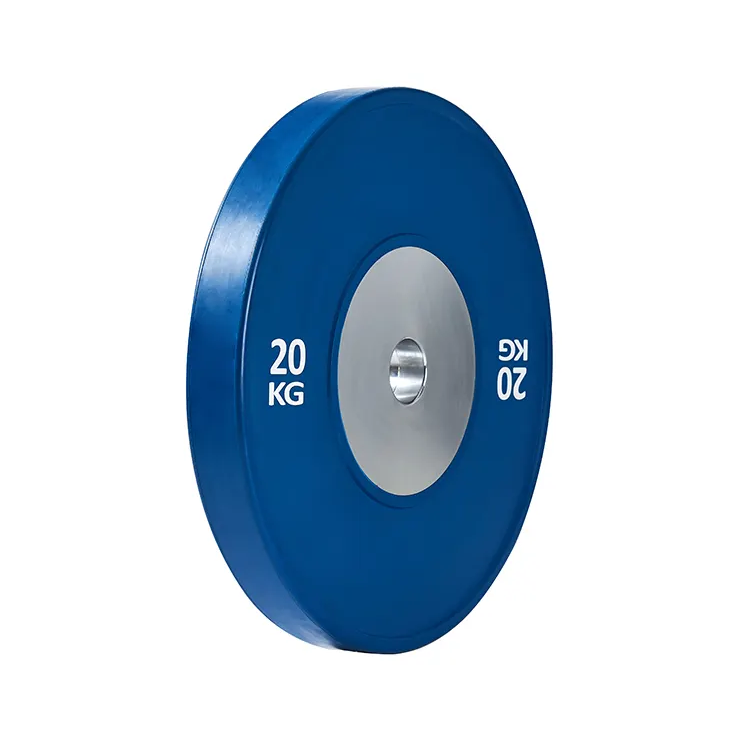
A: Black oxide coatings are widely utilized in various industries due to their excellent corrosion resistance, aesthetic appeal, and enhanced wear-resistant properties. The process involves converting the surface layer of ferrous metals into a durable, blackened oxide layer called magnetite through a chemical reaction. Despite its numerous advantages, it is not without its challenges. Manufacturers and finishers often encounter processing issues that can render subpar results and inconsistent coatings. This article delves into black oxide troubleshooting, exploring the common hurdles faced during application and providing insights into effective solutions. By understanding and resolving these challenges, professionals in the industry can achieve optimal black oxide finishes that meet the highest standards of quality and durability.
One of the first aspects to evaluate when running into issues with your black oxide application is that of your upstream or pretreatment processes. Preparing a surface prior to a black oxide application is critical to achieving a uniform distribution of color, free of splotches and inconsistencies. Alkaline or caustic cleaning solutions are primarily employed for the treatment and removal of organic contaminants; combining a product’s high pH and an elevated operating temperature (~180°F or higher) enables a cleaner to effectively remove and breakdown a broad spectrum of oils and greases that may be present on the part’s surface. Additionally, these cleaners can often contain chelating or sequestering agents that aid in minimizing select inorganic contaminants such as carbon (smut) and mild oxidation (flash rust).
The primary issue within the cleaning step is improper maintenance of the cleaning bath itself. Oil-splitting cleaners are often favored over emulsifying cleaners as they can be more economical in the long run. These products separate or split out the removed contaminants from the cleaning solution, enabling them to float and create a superficial oil layer; this imposes the potential for subsequent contamination of the cleaned parts upon removal from the solution if not properly and routinely addressed. While several methods exist to remove oil layers, overflowing weir systems are among the most effective and efficient. These systems work by constantly flowing the bath over a weir, isolating the mix of the oil layer and excess cleaner into a satellite tank that allows the two components to resegregate before returning the cleaner to the tank.
In addition to the cleaning aspect of pretreatment, surface activation or acid pickling is another crucial step influencing the resulting black oxide finish. Acid activation serves several purposes in preparing the part for blackening; first, it complements the preceding cleaning step by removing any remaining inorganic contaminants from the substrate, including rust, scales, and other metallic impurities that would otherwise inhibit the development of a uniform and adherent black oxide layer. Secondly, the acid step facilitates a controlled etch on the surface of the metal that “activates” the surface of the steel and, depending on the formulation of the acid, can attack and remove certain elemental constituents in the alloy, contributing to the promotion of a darker coloration in the subsequent black oxide step.
Often overlooked or underappreciated is the impact adequate rinsing can have on the outcome of the black oxide finish. Just as the consideration of removing contaminants is essential, so too stands the preventative effort of reapplying or carrying over pollutants between the process tanks. This encompasses previously removed contaminants and the chemistries used to do so, which can cross-contaminate the process tanks in sequence. Maintaining the rinse tanks’ cleanliness mitigates these risks by flushing the parts between active chemical steps and diluting chemical carry-over to introduce minimal drag-out into subsequent process tanks. Ideally, these tanks are continuously flowing to flush out the rinse water and prevent the buildup of pollutants that would otherwise propagate in static rinse tanks. Counterflowing rinses are often utilized as an efficient method to balance net water flow and rinsing efficacy by staggering the rinse tanks to backflow successively, offering an additional level of magnitude of cleanliness for each counterflow rinse stage employed.
Considerations for the black oxide solution are dually critical in troubleshooting issues with the quality of the surface treatment. While the chemistry and process are relatively simplistic, a few key factors should be evaluated to ensure the black oxide solution can function and develop appropriately. Maintaining adequate concentration and temperature of the operating solution ensures that the bath adequately performs to provide consistent results within and between batches.
Unlike other chemical baths that require titrations for control procedures, the concentration of the black oxide chemistry can be largely maintained indirectly through the solution’s boiling point. Black oxide chemistries are saturated salt solutions that typically possess a boiling point of around 283-288°F; maintaining the solution’s boiling point ensures that its constituents remain at appropriate ratios and stabilize the solution’s water content. As the bath operates at temperature throughout the day, water evaporates from the solution causing both concentration and boiling point to elevate. Conversely, as excess water is introduced to the solution, the concentration and boiling point depress. A best practice in maintaining these variables would be with the use of an automated water addition system, which incorporates a thermocouple and solenoid valve to gradually add water to the bath once the temperature surpasses an upper limit; this compensatory measure drives the boiling point back into operating range and restores the solution to equilibrium. Additionally, this method limits the risks of adding too much water too quickly, which can lead to boiling over of the solution.
Another aspect of temperature to be mindful of is the ability of the tank to remain or quickly regain operating temperature throughout processing. Often, people tend to overwhelm the tank with excess parts, leading to a dramatic drop in the solution’s temperature as the steel being processed acts as a significant heat sink to the thermal energy present in the solution. To counteract the drop in temperature, the heat source must regain this energy to return the chemistry to a boil. The primary concern with this scenario is the coinciding loss of convection when the boil dissipates as that is the sole source of agitation for the black oxide solution; losing the convection enables the solution to remain locally static in proximity to the substrate’s surface, providing the opportunity for free iron to deposit on the surface and limiting the ability of the conversion reaction to proceed as intended. This yields incomplete and inconsistent coloring on the surface and can contribute to a rusty appearance on the finished parts. Ideally, the solution’s temperature should not drop more than 5°F below the boiling point, which allows the bath to return to operating temperature within 1-2 minutes, depending on the method of heating and the volume of the solution in the tank; a best practice to avoid overwhelming the tank is not to exceed 1 lb of parts per gallon of solution.
In addition to maintaining the boiling point, monitoring the iron content within the solution is another factor that can significantly impact the appearance of the coloring. Soluble iron is a natural byproduct of the oxidation reaction that occurs with this chemistry and, over time, will gradually build up within the solution. Many black oxide products have an incorporated buffering capacity for iron; however, excess iron will begin to crash out of the solution once that limit has been surpassed. The convections created with the boiling of the solution stir up the iron and leave the parts being processed vulnerable to the excess iron depositing onto their surface, resulting in a red cast that is often difficult to remove. Utilizing a filter basket containing a fine stainless mesh is an effective way to passively collect and remove the excess iron from the bath during routine operation; beyond removing the iron, this method also assists in removing some of the white carbonates that naturally develop as the bath is left exposed to the atmosphere. Extending beyond the daily upkeep, periodic decant and desludging of the tank will also ensure that the chemistry is being maintained for long-term viability and continued use.
Understanding these common challenges and implementing practical solutions is the key to addressing these quality issues. Routine evaluation of these process elements, from the effectiveness of the pretreatment steps to the quality and operation of the active black oxide solution, will enable applicators to proactively identify and address issues before impacting the quality of the application. Working with your chemical provider to better understand your process and provide training for the operators will ensure that you can lower the frequency of quality issues, minimize costly preprocessing and downtime, and ultimately uphold your reputation with your customers.
Connor Callais is an applications specialist for Hubbard-Hall. Visit hubbardhall.com.
The German Association of the Automotive Industry’s VDA Volume 19 is the first comprehensive standardization document for characterizing the cleanliness of products within the automotive industry’s quality chain.
How do you clean white lime scale and rust spots on galvanize?
How to use it for planning, preventive maintenance and troubleshooting.
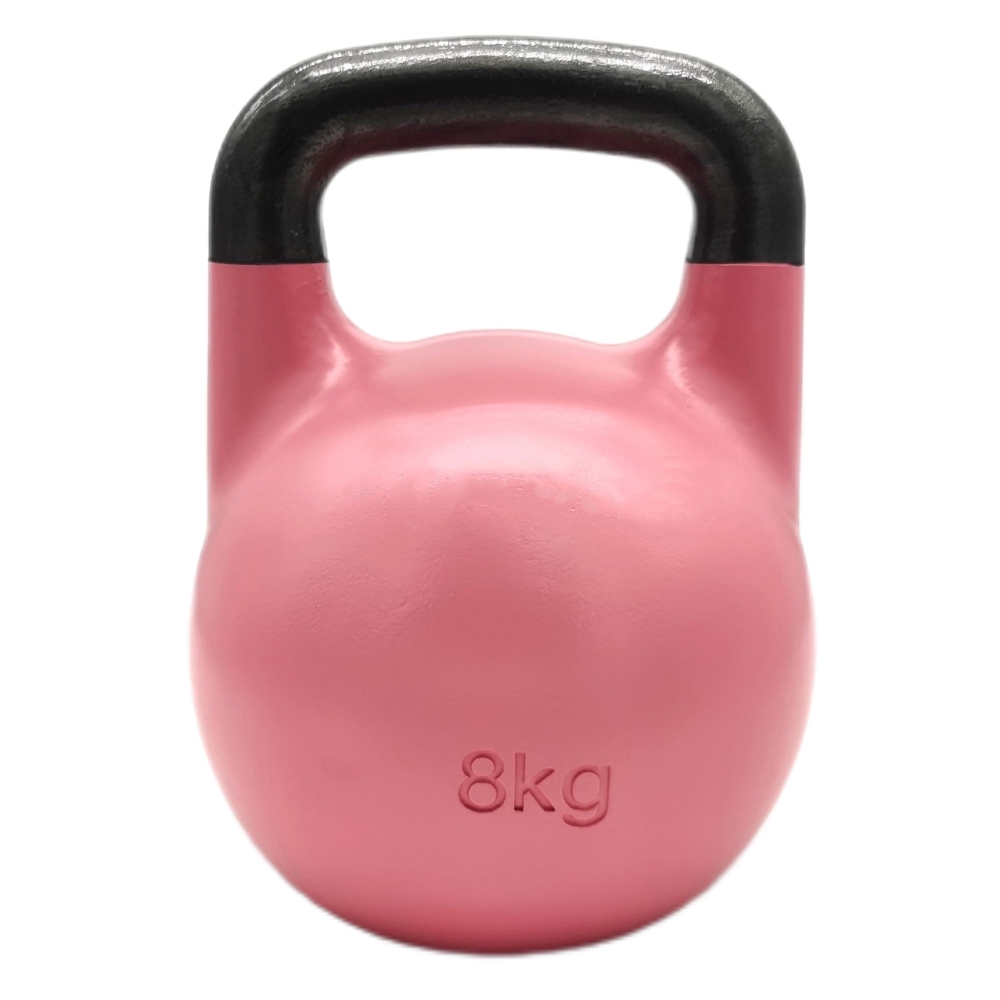
Polypropylene Rope For Swing Copyright © 2024 Privacy Policy [Log On]