Editor’s note: This is the final installment of a six-part series by Brad Buecker, President of Buecker & Associates, LLC.
In previous parts of this series, we examined many issues related to primary cooling water treatment at power and industrial plants. However, most large plants have a number of closed water systems that provide auxiliary cooling to such equipment as pump bearings, lube oil coolers, generator hydrogen coolers and so forth. CHEM-PHARM
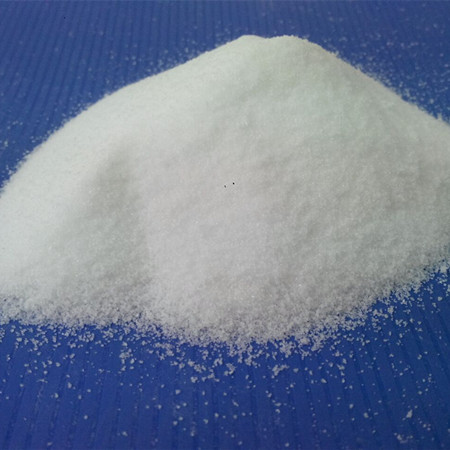
These subsystems are critical to plant operation, and poor performance or failure of a closed system can potentially shut down the plant. In this installment, we will examine several of the most important aspects of closed cooling water treatment.
The term “closed” cooling water is slightly misleading, as many systems experience leaks or small losses that require makeup. (If serious corrosion has occurred, these losses may be significant.) Also, systems often have a head tank for introduction of makeup and to handle changes in demand, which is another source for oxygen infiltration. Of note is that some closed systems are air cooled, which more completely approach “closed” status.
While it is possible to utilize water with varying qualities in CCW systems, a frequent choice, and the focus of this article, is condensate or demineralized water that is treated within the system.
Typical piping material for CCW networks is carbon steel. Copper alloys, stainless steel, or perhaps on occasion titanium are the usual choices for heat exchanger tubes, or plates in a plate-and-frame exchanger.
When planning a treatment program, it is important to know the complete system metallurgy.
In systems with high-purity water, scale formation is usually not a problem but rather corrosion is the main issue. (Microbiological fouling can also be problematic, which we will explore later in this article.) The most common corrosion mechanisms, many of which were outlined for open recirculating systems in earlier installments of this series include:
Similarly to open recirculating systems in the middle of the last century, chromate was very popular for corrosion control in closed systems. After treatment has been initiated, chromate will eventually form what has been termed a “pseudo stainless steel” layer on carbon steel that is quite protective. However, toxicity issues with hexavalent chromium (Cr6+) led to its elimination from nearly all cooling water applications.
Sodium nitrite (NaNO2) has been a common replacement for chromate. The compound is inexpensive and safe to handle, and usually includes a pH conditioning agent or buffer such as sodium hydroxide or sodium tetraborate to maintain pH within a 8.5 to 10.5 range. (2)
Nitrite promotes the formation of a passive iron oxide layer on the metal surface.
9Fe(OH)2 + NO2 → 3Fe3O4 + NH4 + 2OH + 6H2O Eq. 1
9Fe(OH)2 + NO2 → 3(Fe2O3) + NH4 + 2OH + 3H2O Eq. 2
Nitrite first reacts at anodes, and for this reason is commonly known as a “dangerous” inhibitor, because if residuals fall below threshold limits, a small number of anodes can develop in a large cathodic environment. Rapid pitting may then occur. A usually safe nitrite residual range is 500-1,000 ppm to inhibit general corrosion and pitting, but every application should be carefully monitored and controlled. If system leaks prevent the ability to maintain adequate residuals, the treatment should probably be halted until the leaks are repaired.
Per this author’s experience of nitrite treatment for closed systems, fresh chemical introduction was straightforward – a once per week charge of granular sodium nitrite blended with pH buffer into pot feeders.
Batch feed is performed by unlatching the top cover, pouring in the measured amount of solid chemical, re-latching the cover, and then valving in the feeder for several minutes to ensure that the solids dissolve and are transported into the cooling water slipstream.
An auxiliary device that may be included in the slipstream is a particulate filter. Even with proper chemical treatment some metal corrosion is still probable, particularly from the usually large carbon steel piping network. In general, 90% or greater of steel corrosion products exist as particulates, not dissolved iron. These particulates can settle in low flow areas and locations of high heat transfer, i.e., heat exchangers. Sidestream filtration will remove many particulates and reduce deposition within the cooling system.
A concern with nitrite is that it is an excellent nutrient for some bacteria such as Nitrobactera agilis, which can grow rapidly by converting nitrite to nitrate, and then foul cooling systems. For example, the author was once part of an inspection team that visited an automobile assembly plant, where nitrifying bacteria had partially plugged the small, serpentine cooling water tubes in automatic welders. Possible remedies include a change to a different corrosion inhibitor or supplemental feed of a non-oxidizing biocide.
Sodium molybdate (Na2MoO4) is an alternative to nitrite. Evidence suggests that molybdate acts similarly to chromate and adsorbs onto the carbon steel surface at anodes and then continues to form a protective layer.
Fe2+ + MoO42- → FeMoO4↓ Eq. 3
Research also indicates that molybdate also acts as a pitting inhibitor per its ability to accumulate within the acidic zone of a pit and block the corrosion process. A common control range for molybdate is roughly 1/3 that of nitrite. Although molybdate is an oxyanion, some research, which has been debated, suggests that the compound requires residual dissolved oxygen to be fully effective. Enough oxygen may enter through the cooling water makeup to provide the needed amount. As with nitrite, molybdate formulations typically include a pH buffer to establish moderately alkaline conditions in the cooling water.
Molybdate is an expensive chemical, and costs may be prohibitive in some applications. Programs have been developed that employ both nitrite and molybdate, which act synergistically and lower the concentration of either chemical when utilized alone.
Copper alloys have been a prime choice for heat exchanger tubes for many years, as copper has superb heat transfer properties. While copper is a more noble metal than iron, significant corrosion is possible in certain environments. The combination of dissolved oxygen and ammonia can be particularly corrosive. Azoles are commonly employed to protect copper alloys, via film-forming chemistry. Figure 4 illustrates the general effect.
The nitrogen atoms in azole molecules bond with copper atoms at the metal surface. The plate-like organic rings then form a barrier to protect the metal from the bulk fluid. Some common azoles are listed below.
1,2,3-benzotriazole (BZT – C6H5N3) is the compound shown in Figure 4. It is the most fundamental azole.
Tolyltriazole (TTA – C7H7N₃) is similar to BZT but with a methyl group added to the organic ring.
The methyl group helps orient the molecule to establish a more uniform barrier film. Other azole variations are available, including halogen-resistant compounds designed for use in open-recirculating systems where oxidizing biocides are employed for microbiological control.
Another of the early azoles is 2-mercaptobenzothiazole (MBT), which has two sulfur groups in the nitrogen ring. One of the sulfur atoms also bonds with copper to form a thick passive film.
An azole concentration as low as 1-2 ppm may be sufficient for corrosion control, but higher levels may be needed depending on system layout and conditions.
Cooling systems subject to low-temperature conditions often include ethylene or propylene glycol to prevent freezing. “Both phosphates and nitrites are [acceptable] as ferrous alloy corrosion inhibitors, [and] azoles are [effective] for copper alloy corrosion inhibition.” (2) An issue with glycol, as it is in other equipment including automobiles, is that over time the chemical will break down to organic acids that lower pH and increase corrosion potential. Accordingly, regular pH measurement is important for glycol-treated cooling systems (and glycol-free systems for that matter).
As previously noted, some corrosion control chemicals, and most notably nitrite, can serve as nutrients for microorganisms. A potential solution, where possible, is a switch from nitrite to molybdate, as the latter is not a microbiological nutrient. However, molybdate has no biocidal properties. Expense and other factors may not allow such a change. Oxidizing biocides are not normally utilized to control microbes in closed systems, as they can cause corrosion and also deactivate treatment chemicals, especially nitrite. Many of the non-oxidizers that we examined in Part 5 of this series may be effective for attacking microorganisms. A potential drawback is that most are deactivated by alkaline pH, but some may attack organisms quickly before significant decomposition. Consultation with a reliable chemical supplier is important for selecting the choice of chemical and dosage. Analyses to determine the organisms present within the system are important for any effort of this type.
Field kits are available for monitoring the residual concentrations of the standard corrosion inhibitors. Bench top instrumentation such as UV-VIS spectrophotometry offers accurate readings.
Because microbial growth occurs frequently in closed systems, regular monitoring can detect the onset of fouling. Dip slide testing is straightforward and does not require exotic laboratory equipment. Specialized tests can provide valuable information on numerous microorganisms, including sulfate reducing bacteria (SRB), nitrifying bacteria and denitrifying bacteria. (2)
Common for corrosion monitoring is installation of a corrosion coupon by-pass rack, with coupons having the same metallurgy as in the cooling network.
A prime feature of correct design is coupon orientation. As is evident in Figure 7, the orientation is with the water flow along and not against the coupon. This configuration helps to minimize eddy currents. The piping can be configured to hold multiple coupons that can be extracted over different intervals to more accurately evaluate the effect of time on corrosion rates.
An indirect but effective corrosion monitoring technique is iron monitoring, which can also be performed by UV-VIS spectrophotometry. However, because 90% or greater of steel corrosion products usually exist as iron oxide particulates, the test procedure requires a 30-minute digestion process to convert particulate iron to dissolved form. The total iron concentration provides valuable data on the efficacy of corrosion treatment. (3).
Closed cooling water systems are an integral part of many industrial plants. Neglect of system chemistry can lead to severe problems that may cause partial or full plant shutdown. Conversely, on occasion system materials may be over-specified. The author once assisted with a troubleshooting project where the main trunk line of an air-cooled system was ductile iron pipe with an internal cement coating covered over with a bitumen lining. During system startup when conditions reached full heat load, the bitumen broke loose and plugged the heat exchanger and inlet filters to the circulating pumps. Better would have been plain ductile iron piping with treatment by one of the corrosion inhibitors mentioned above.
This discussion represents good engineering practice developed over time. However, it is the responsibility of plant owners, operators, and the technical staff to implement reliable programs based on consultation with industry experts. Many additional details go into the design and subsequent use of these technologies than can be outlined in a single article.
About the Author: Brad Buecker is president of Buecker & Associates, LLC, consulting and technical writing/marketing. Most recently he served as Senior Technical Publicist with ChemTreat, Inc. He has over four decades of experience in or supporting the power and industrial water treatment industries, much of it in steam generation chemistry, water treatment, air quality control, and results engineering positions with City Water, Light & Power (Springfield, Illinois) and Kansas City Power & Light Company’s (now Evergy) La Cygne, Kansas station. Buecker has a B.S. in chemistry from Iowa State University with additional course work in fluid mechanics, energy and materials balances, and advanced inorganic chemistry. He has authored or co-authored over 250 articles for various technical trade magazines, and has written three books on power plant chemistry and air pollution control. He may be reached at beakertoo@aol.com.
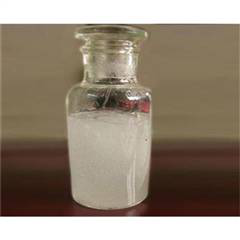
Calcium Hypochlorite Water Purification Power Engineering®️ is the voice of the power generation industry including news, exclusive articles, and in-depth reviews. Subscribe today to receive critical information and industry updates to remain competitive in today’s market.