2013 marks the centenary of the invention of stainless steel. TM talks to UK manufacturers who process and use the material about its continuing significance in today’s world. Jane Gray reports.
A century after its discovery, the UK produces almost 330,000 tonnes of stainless steel in a year. Around 213,000* tonnes is used by manufacturers in sectors from nuclear energy components through catering equipment, healthcare, construction, domestic appliances, automotive, oil & gas, renewable energy and more. It is a vital staple for thousands of UK manufacturing and engineering firms. Steel Sheet 304
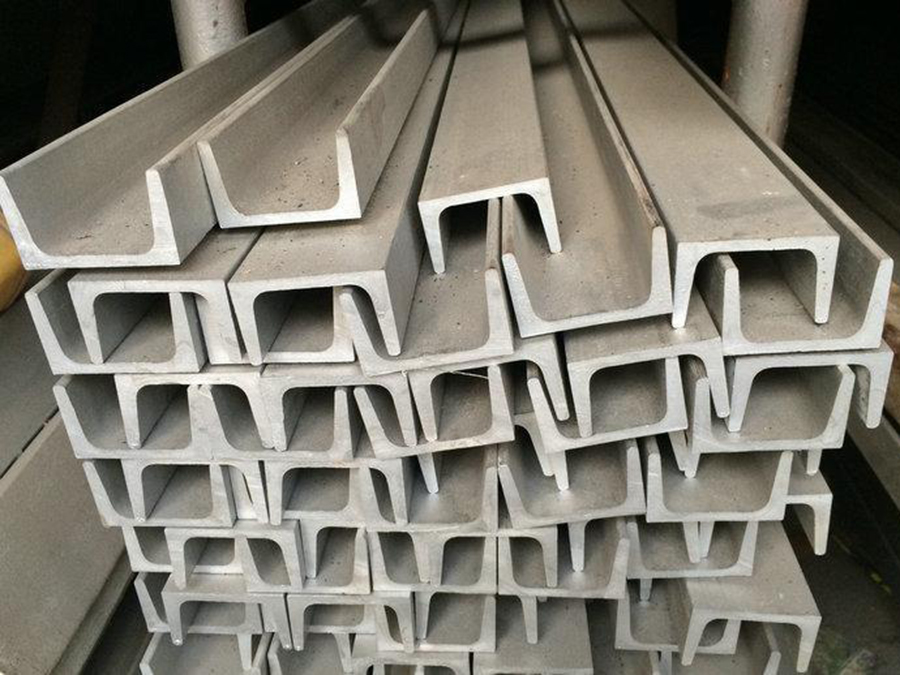
One of the manufacturing sectors to use stainless steel most prolifically is the catering equipment sector. Catering equipment manufacturers in the UK use between 12,000 to 14,000 tonnes of stainless steel each year.
Williams Refrigeration, a subsidiary of AFE Group, is based in Kings Lynn, Norfolk and employs around 300 people at its 33,000sq metre site. Stainless steel is the core material used in its commercial refrigeration products. “It is ideal for our customers because it is hard wearing and food safe,” says Malcolm Harling, the company’s sales and marketing director. “It is far easier to keep clean than plastics, for example – many of which can actually wear and degrade with the potential that fragments get into food.”
The company uses three of the most common grades of stainless steel: 304, 430 and 441. “The choice of grade will depend on the customer specification and the environment it will be used in,” says Harling. “Our customers who are involved in the production of baked goods, for instance, need to take the high likelihood of enzyme corrosion in a bakery into account. This means using a higher grade like 304.”
Williams Refrigeration sources sheet stainless steel both in the UK and abroad as availability and prices dictate. Increasingly, however, the preference is to source as locally as possible, says Harling. “It helps to cut down our carbon footprint which is very important to us and, as a British manufacturer, we are looking more and more to buy as many of our components and materials as possible within the UK. It is not always possible, however.”
Is there an opportunity for British manufacturing to leverage the stainless steel centenary to its advantage? “I think there is,” states Harling. “It wasn’t something that I was aware of but now that I am I will be looking into possible marketing options.”
What makes stainless steel so special? Its resistance to corrosion means that it is a durable metal which will not oxidise (rust) or react with many substances, from bodily fluids to beer. It is also resistant to heat, therefore suitable for use in environments from up to 1,200°C down to -196°C depending on the grade of steel. And it is cheap compared to other, specialist, non-corrosive alloys which have been discovered more recently. Chromium is a key ingredient that makes this steel so popular. Chromium reacts with oxygen in the air to form a passive chromium oxide film on the surface of the metal and, in general, the higher the chromium content the more resistant to corrosion.
Harry Brearley is widely attributed with the invention of the first true stainless steel, which had a chromium content of 12.8%.
There are now around 100 grades of stainless steel commercially available spread across four main family groups; martenistic, ferritic, austentic, and duplex. These have varying quantities of other alloying metals (nickel, titanium, copper) added to them, as well as carbon and nitrogen, to enhance characteristics such as corrosion resistance, ductility, formability and weldability.
Brearley’s invention is a landmark in British industrial history which has made his home town of Sheffield renowned as a global centre for metallurgy. This year Sheffield will be the focal point for several events to celebrate the importance of stainless steel to its economic heritage and its future. A key event for stainless steel-using companies is the Harry Brearley Stainless Steel Centenary Conference and Exhibition which will be hosted by the British Stainless Steel Association (BSSA) and the Sheffield Metallurgical and Engineering Association on June 12.
These institutions are keen to emphasise that while stainless steel production is a global industry, with China now unsurprisingly the largest producer, the home town of stainless steel remains at the heart of developments in production technologies and applications.
For example, the world’s largest stainless steel producer and distributor, Outokumpu, a sponsor of the Brearley conference, employs around 600 people in Sheffield at its melt shop, bar mill and service centre. Outokumpu sells 80,000- 100,000 tonnes of stainless steel to British manufacturers every year (p32). In 2010 the company completed an investment of Eu10 million to establish an integrated manufacturing route for small bar and reinforcing bar products. This new line compliments Outokumpu’s existing melt shop and wire-rod mill.
What do we mean by ‘UK production’ of stainless steel?
The 330,000-odd tonnes of stainless steel produced in the UK annually is a tiny fraction of total global production. It is also a massive reduction on the amount of stainless steel produced in Britain in the past.
Outokumpu maintains a stainless steel melting facility in Sheffield which has potential operational capacity of 400,000 tonnes per annum. This is the UK’s only large scale stainless steel melt shop however.
Outokumpu also has hot rolling facilities for stainless steel rod, using steel from the Sheffield melt shop. Hot rolling of stainless steel bar is done by an Outokumpu partner. Tata Steel also has stainless steel bar and rod rolling facilities in Rotherham and Scunthorpe. In December 2012 Tata Steel completed a £1.5m pound investment programme to improve the quality of output at these plants.
Other stainless steel processing includes cold drawing of wire at companies like Stocksbridge-based Fox Wire. While hot and cold rolling of ‘flat product’ has entirely disappeared from the country, finishing facilities for slitting, cutting, polishing and laser profiling have a robust presence.
Meanwhile, at the Nuclear Advanced Manufacturing Research Centre in Rotherham, important research into deephole boring techniques for stainless steel components in the nuclear industry is ploughing ahead. A big challenge for this project is to develop boring techniques which can cope with the high ductility of the 304 stainless steel used in nuclear applications. High ductility is needed to avoid “neutron embrittlement” during use in the nuclear cooling process, but it increases the risk of clogging and exploding drill bits during the machining process.
Tapping into growing industrial and societal concerns about the sustainability of commonly used materials, the conference will also want to emphasise the sustainable credentials of stainless steel which is 100% recyclable. Indeed the BSSA claims that every new melt of stainless steel made today contains around 65% recycled material. The association is also closely tracking investment in the development of various renewable energy technologies in the UK. Stainless steel is used, to varying degrees, across many of the technologies which may become integral to our energy generation infrastructure in the future, including tidal, biogas, solar and carbon capture and storage.
Users speak out: Ancon Building Products
Modern art and architecture has made stainless steel a ubiquitous part of many cityscapes around the world – both as a structural and aesthetic feature.
Ancon, with sites in Sheffield and Deeside, supports around 230 manufacturing jobs in the UK and buys around 6,000 tonnes of stainless steel each year in plate, slit coil, wire and bar.
The company, which won a Queens Award for Innovation in 2012, designs and manufactures a range of structural products for use in construction and civil engineering applications, from housing through to large civil projects and tunnels. Peter McDermott, operations director at Ancon, says that the material is ideal for its resistance to corrosion and its strength, and also because it is easy to fabricate.
Ancon sources its stainless steel from the UK, Europe and beyond. Purchasing decisions, particularly for higher volume products, have little thought for patriotism says Mr McDermott. “For basic ‘mill direct’ products, sadly it isn’t generally too important where the material is sourced from. It is more important to have the correct supply chain in place to ensure quality, competitiveness and reliability of supply.” However, when it comes to more bespoke applications and products, UK suppliers do have the chance to carve out a niche, he says. “In these cases it is important to have flexible customer-focused processors or suppliers in the UK to be able to offer the flexibility and service we need to meet our customers’ requirements.”
As an active member of the close-knit industrial community around Sheffield, Ancon is very aware of this year’s centenary celebrations and is keen to promote it. “The centenary is a great opportunity to promote the benefits of stainless steel over other materials and the contribution it has made to society over the last 100-years,” says Annabelle Wilson, Ancon marketing manager. “This links nicely to our company history and product range. We make high integrity fixings used where maintenance is either impractical or impossible, so stainless steel is the obvious and most costeffective choice”.
Through 2013, Ancon’s website, marketing and communications will display the ‘100 years of stainless steel’ logo.
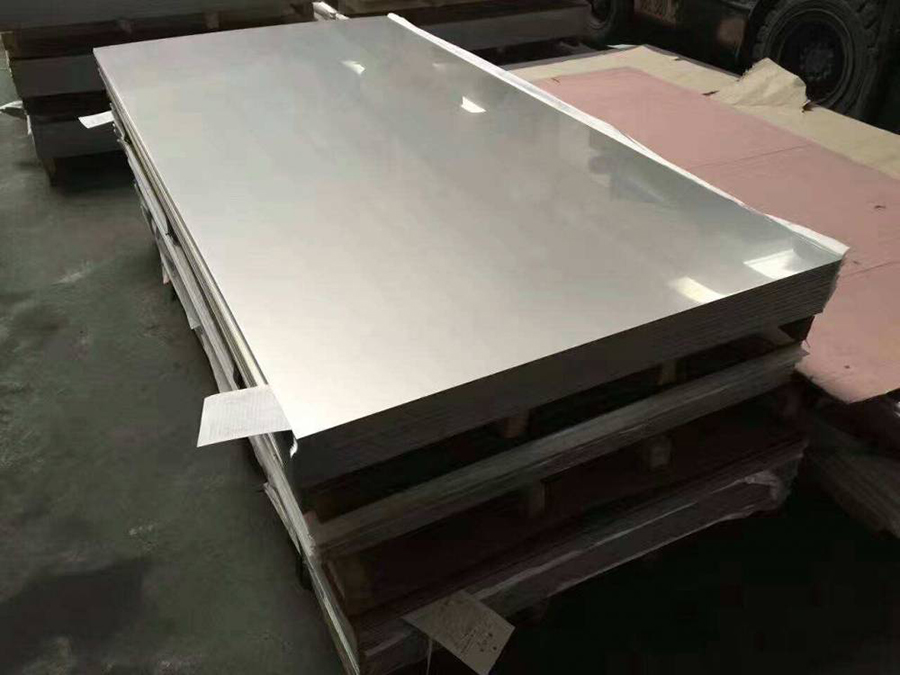
304 Stainless Steel Bar Stock Promoting the usefulness of stainless steel in new applications is at the core of BSSA’s remit, and as part of its centenary activities it is running an email campaign to businesses and the general public that explains one application a week throughout 2013. To sign up to the ‘100 Not Out’ campaign go to www.bssa.org.uk.