EVs have electric motors. Conventional cars have engines. From the driver’s seat, very few vehicle owners have more than a passing understanding of what is powering their vehicle or how it works.
Four-stroke internal combustion engines operate by exploding a small amount of vaporized gasoline in a confined space called a cylinder. The force of the explosion pushes a piston, which turns a crankshaft, which spins gears in a transmission, which turns a driveshaft, which turns gears in a differential, which turns an axle, which makes the wheels go around to move the vehicle forward. YE5 Series

This process is memorialized on a T-shirt available at any Harley Davidson dealer which reduces the entire process to its simplest terms — Suck, Push, Bang, Blow. That pretty much sums up how most internal combustion engines work. Some engines are better at high speeds and others are better at low speeds.
There are also various types of electric motors, but few drivers know the difference. We get in, push the exhilerator, the car moves forward, and that makes us happy. What more do we need to know? Actually, there’s a lot going on beneath our right foot. Here’s more about that, thanks to the folks at Top Speed.
There are three types of electric motors commonly used by electric car manufacturers — synchronous permanent magnet, electrically excited synchronous, and asynchronous induction. They each have advantages and disadvantages. (There are other types of electric motors for special use cases that will not be discussed here.)
In synchronous permanent magnet electric motors, the rotor is embedded with permanent magnets. When an alternating current is supplied to the stator, it generates a rotating magnetic field magnetic which interacts with the permanent magnets in the rotor to create a synchronous rotation which produces the torque that turns the wheels of an electric vehicle. The synchronized rotation ensures optimal power conversion, maximizing efficiency and performance in a compact package.
The velocity of the vehicle is modulated by varying the frequency of the AC supplied to the motor. Advanced control systems in electric cars facilitate meticulous control over the motor’s operation, allowing for precise adjustments to speed and torque based on driving conditions, enhancing the vehicle’s adaptability and responsiveness.
Synchronous permanent magnet electric motors are known for their high power density and efficiency,which makes them an optimal choice for electric cars where space and energy conservation are crucial. They are commonly used to power the rear wheels of electric cars manufactured by Volkswagen and Tesla. They were also used by General Motors in its Volt and Bolt cars. Hyundai uses them on the front and rear of its dual motor electric cars.
One drawback to these motors is that permanent magnets usually require rare earth minerals, which are expensive and may have sustainability drawbacks due to the way in which they are mined.
Electrically excited synchronous motors receive alternating current to the stator, which creates a rotating magnetic field. Direct current is supplied to the rotor to generate a magnetic field that aligns synchronously with the rotating field of the stator. This synchronized interaction between the rotor and stator magnetic fields produces torque to propel the car.
The vehicle’s speed and torque are precisely controlled by adjusting the frequency and amplitude of the supplied AC, enabling precise manipulation of the motor’s output to suit varying driving conditions. Advanced electronic controllers interpret the driver’s inputs, modulating the motor’s operations to ensure responsive and smooth driving dynamics.
Electrically excited synchronous electric motors are known for their flexibility and adaptability. They do well in use cases that demand high torque and power, ensuring peak performance across diverse driving environments. They embody adaptability and power while adapting their operational characteristics to the demands of a particular vehicle for optimal performance. BMW uses them to power most of its electric cars.
Asynchronous induction electric motors are based on the principles developed by Nikola Tesla. They rely on three phase alternating current and are distinguished by the absence of brushes and commutators, which reduces maintenance and enhances longevity.
Alternating current is applied to the stator windings, which creates a rotating magnetic field that induces a current in the rotor due to electromagnetic induction. As the rotor never reaches the synchronous speed of the stator’s magnetic field, it is identified as an asynchronous function.
When used in an electric car, the speed of the motor is controlled by varying the frequency of the AC supplied to the stator and manipulated through advanced electronic control systems, which allows precise control over the vehicle’s motion. Volkswagen and Tesla use asychronous induction to power the front wheels of their electric cars.
Asynchronous induction motors are known for their robustness and efficiency, which makes them ideally suited for varied driving conditions. They can generate substantial torque at low speeds, which is beneficial for starting and low speed maneuvers, while maintaining efficiency at high speeds. Their ability to operate under diverse load conditions with minimal wear makes them a perfect choice for electric vehicles because they combine performance with reliability.
According to an article on LinkedIn, induction motors have some disadvantages, such as low efficiency, power factor, and torque. They also produce more heat, noise, and slip than synchronous motors. By contrast, synchronous motors have high efficiency, power factor, and torque.
Choosing between synchronous and induction motors depends on several factors, such as the required speed, torque, power, load, and application. Generally, synchronous motors are more suitable for applications that need constant speed, high power, or precise control, while induction motors are more suitable for applications that need variable speed, low power, or simple operation.
Motor efficiency is the ratio of the mechanical output to the electrical input expressed as a percentage. It depends on several factors, such as the design, size, speed, load, temperature, and losses of the motor. Synchronous motors have higher efficiency than induction motors, especially at high loads and speeds. Induction motors have higher losses, especially at low loads and speeds.
All electric motors for electric vehicles require sophisticated motor control systems. Synchronous motors require more complex and expensive control devices than induction motors, such as variable frequency drives, slip rings, or brushless excitation systems. Induction motors require simpler and cheaper control devices than synchronous motors, such as rheostats, capacitors, or soft starters.
What does this all mean? Quite simply, that manufacturers have choices when it comes to powering electric vehicles, and those choices will determine the driving characteristics of the cars they build. They have to balance cost, power, and efficiency to build compelling electric cars that will put smiles on the faces of their customers for years and years of all electric motoring.
Steve writes about the interface between technology and sustainability from his home in Florida or anywhere else The Force may lead him. He is proud to be "woke" and doesn't really give a damn why the glass broke. He believes passionately in what Socrates said 3000 years ago: "The secret to change is to focus all of your energy not on fighting the old but on building the new."
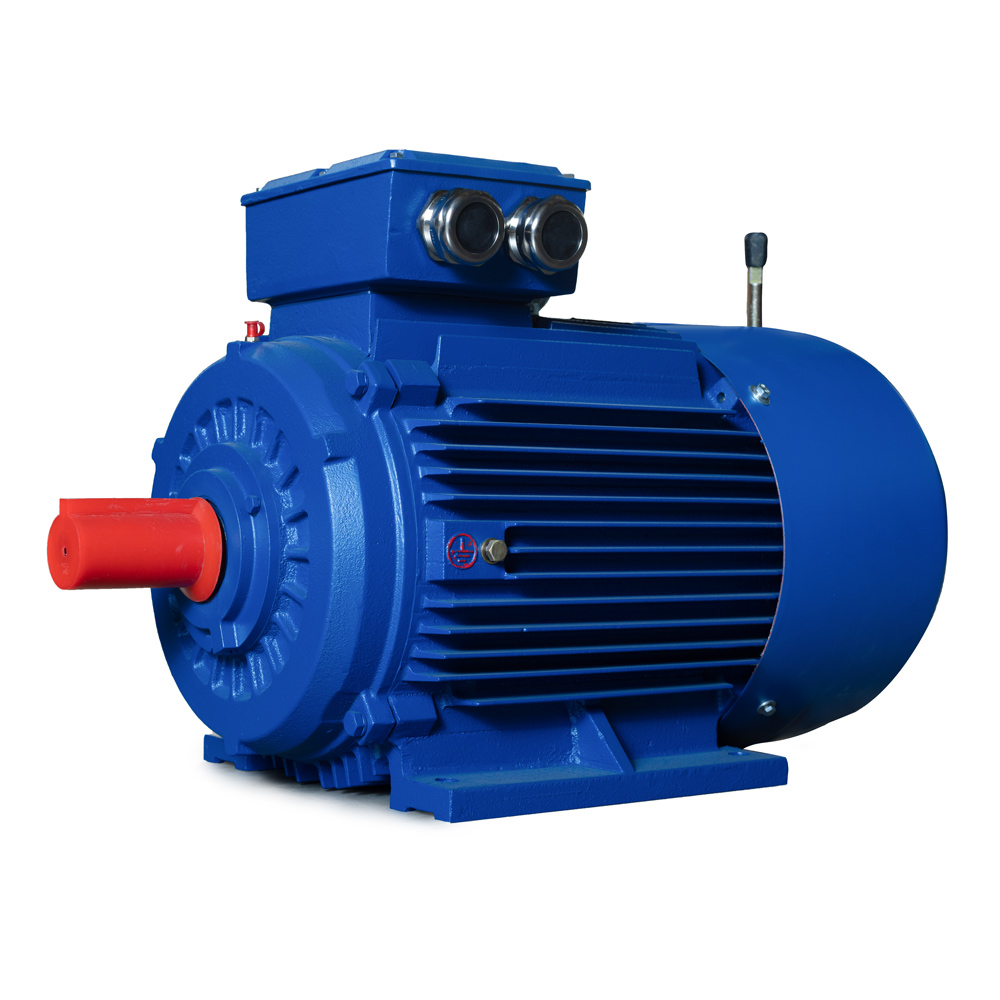
Energy Saving Steve Hanley has 5290 posts and counting. See all posts by Steve Hanley