by Dan Shaw, Technology Manager, Structural Adhesives and Michael Williams, OEM Marketing Manager, Henkel Corp.
Although polyolefin based plastics such as PE, PP and LDPE have proven useful in innumerable applications, they are difficult to bond with adhesives. PVC Membrane
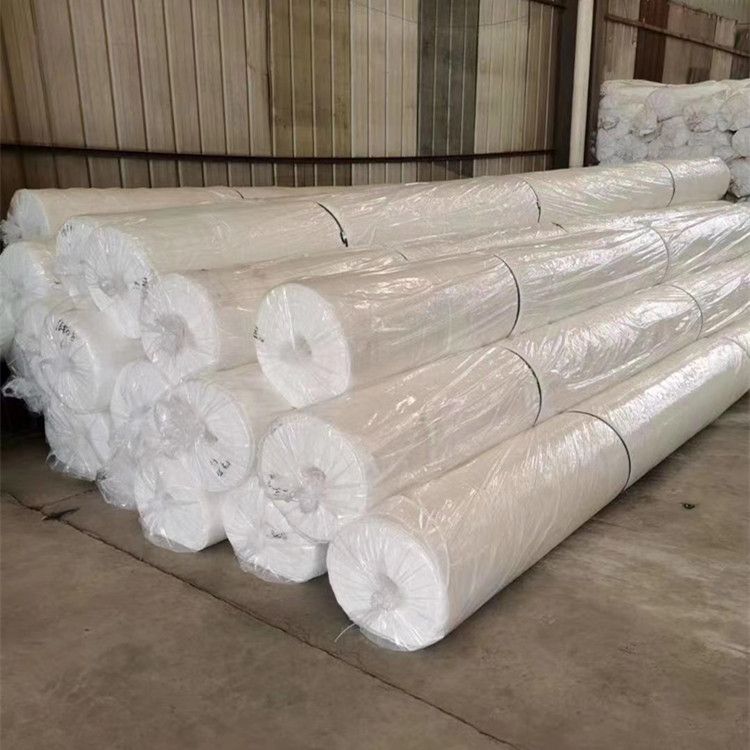
Traditional liquid adhesives do not wet out well on low-surface-energy polyolefin plastics. To achieve a robust bond in any joining application, good surface contact is required between the adhesive and substrates; the adhesive must spread across or “wet out” the plastic surface. To effectively wet out a surface, the adhesive’s surface energy must be equal to or lower than the surface energy of the substrate to be bonded.
These traditional adhesives very easily wet out on substrates like metals and high surface energy plastics such as ABS and polycarbonate, achieving a strong and lasting bond over a large bond area. But with polypropylene, polyethylene, nylon and other low surface energy plastics, traditional adhesives remain as droplets or beads, never covering the substrate surface and maximizing contact area.
If an adhesive doesn’t adequately wet the surface and achieve intimate molecular contact with the two substrates to be bonded, adhesion will be weak and the bond will not be robust. To solve this problem, manufacturers have long relied upon surface preparation or surface treatments to enhance adhesion and bond strength. Surface preparation methods for polyolefin plastics include both chemical and physical treatments designed to increase reactivity and roughness on the surface of the substrate.
Common surface treatment methods include: • primers that chemically activate the surface of the plastic; • etching or surface roughening that increases the surface area on the bond site and adds a mechanical component to the bond; and • energy treatments that expose the plastic to plasma, corona or flame, increasing the surface energy of the substrate and removing surface contaminants that inhibit adhesion.
While surface treatment techniques can effectively increase bond strength, they are an extra step in the manufacturing process, can be expensive and time consuming, and often require handling and storage of hazardous materials to be effective on polyolefins. Energy treatments are temporary—a short time after exposure, the polyolefin reverts to its original low surface energy.
Instant adhesives or cyanoacrylates are the most commonly used adhesives for bonding polyolefin plastics. To achieve a strong bond, substrates must be treated with a primer prior to adhesive application. Once cured, instant adhesives are typically brittle and can fail in applications that must withstand shock or impact.
A polyolefin bonder To help meet design and production challenges related to bonding low surface energy plastics, Henkel Corp. introduced a new adhesive technology to effectively bond polyolefins without the time and expense of priming or complex surface treatments.
This adhesive, Loctite 3035 Polyolefin Bonder, is a two-part structural acrylic that achieves superior bond strength on HDPE, LDPE, UHMWPE, PP, ABS, nylon, polycarbonate, PVC, epoxy, steel and aluminum.
Offering good environmental resistance in a range of end-use applications, the adhesive reliably and consistently performs on appliances, ATVs, outdoor power equipment, plastic pipes and vehicles. In such applications, the adhesive provides excellent resistance to moisture, salt fog and non-polar solvents such as diesel, gas and motor oil. The adhesive withstands a variety of stresses including shear, impact and shock. Shear strength is 1600 psi on HDPE, 600 psi on LDPE, 1200 psi on PVC, and 400-650 psi on metals.
The polyolefin bonder mixes easily and fixtures to many plastics and metals in less than 15 minutes without surface preparation or primers. Fixture time is the amount of time it takes for the adhesive to cure to the point where a part can be moved without compromising the bond, and varies with the substrate. Full cure happens in just 24 hours at room temperature. The adhesive’s work life is 2 to 4 minutes with a shelf life of one year.
The 50 ml cartridge package delivers an accurate 1:1 mix ratio to ensure proper cure to a high-strength bond every time. The two parts of the adhesive have a viscosity of 7500 and 60,000 cps. This low viscosity allows the material to be dispensed easily with either manual or pneumatic applicators.
When fully cured, the adhesive delivers a flexible and impact resistant long-term bond.
Similar polyolefin bonding adhesives are available on the market, but require fixture times as much as four times longer. These extended fixture times can add to the cost of the manufacturing process as parts must be stored or racked while the adhesive cures to fixture strength. A faster fixture time can reduce or eliminate the bottleneck related to racked work in progress.
Real world applications The 3035 Polyolefin Bonder is has been available on the market for less than a year, and has already proven its suitability in a range of manufacturing applications, from communications devices to medical equipment to vehicle assemblies.
In the assembly of wireless communications devices, the adhesive has replaced cyanoacrylate adhesive technology for bonding together the thermoplastic vulcanizate components that make up the case for the battery pack. The thermoplastic vulcanizate substrate is as flexible and durable as rubber, designed to withstand constant exposure to rough handling. But thermoplastic vulcanizates are extremely difficult to bond. The manufacturer was using a cyanoacrylate adhesive to bond the case, but the assembly’s failure rate in underwater pressure testing was 30%, a number too high to tolerate.
The new polyolefin bonding adhesive effectively bonds thermoplastic vulcanizate, matches the durability of the substrate and withstands temperature extremes and harsh end use environments. Since the manufacturer changed adhesive technologies, failures have dropped to zero on exposure to the same underwater pressure test.
The polyolefin bonder is also finding favor in medical device assembly applications. For example, the manufacturer of a therapeutic breathing machine has replaced methyl methacrylate adhesive technology (MMA) for bonding aluminum to polypropylene in their motor enclosure assembly process. Because the adhesive is clear, it provides a more aesthetically pleasing bond line. Its 15 minute fixture time dramatically speeds the component assembly process over MMAs, which fixture in 30 minutes.
Because ultra high molecular weight polypropylene (UHMWPP) absorbs no moisture, has a very low coefficient of friction and is self lubricating, it is very difficult to bond. But this substrate works on equipment and devices exposed to wash down. Before the new polypropylene bonding adhesive, manufacturers used mechanical fasteners to attach UHMWPP to other substrates, often steel and other metals. But contaminants and bacteria can build up in crevices between the fastener and the substrate, compromising the safety of the process. The new polypropylene bonding adhesive has replaced fasteners for attaching UHMWPP parts on equipment exposed to wash down. It permanently secures UHMWPP and creates a complete seal impervious to microorganisms.
Plastic pipes carry a variety of fluids, from water to gasoline, and pipe manufacturers often need to join multiple polyethylene pipes in a series. A splice is made at the end of one pipe and a collar is bonded to attach the next pipe using the polyolefin bonding adhesive. The adhesive is also used to bond and seal fiberglass reinforced plastic fittings onto polyethylene pipes. These fittings are used as flanges that secure other components. In all these applications, the adhesive must fully seal the joint to prevent leakage and must resist caustic chemicals that could damage the assembly.
The PO bonder can be used on motor vehicles and personal watercraft for similar assembly challenges. On the dashboard assembly of a heavy duty truck, the polyolefin bonder is being used to attach the polypropylene glove box to the backside of the ABS dashboard. Once installed, this glove box assembly carries weighty contents, sits perilously close to the engine and is exposed to heat, heavy vibration and tensile/peel stresses. The adhesive that was being used for this application withstood the harsh operating conditions but took 6 hours to fixture, slowing the assembly process. By changing to the new PO Bonder, the manufacturer reduced fixture time for the PP/ABS assembly to just 2 hours and made it possible to manufacture and ship the dashboard assemblies in the same business day.
Personal watercraft applications for the polyolefin bonder are similar to those found on motor vehicles. The adhesive bonds and seals trays and storage compartment doors to the body of the watercraft, and is also used to bond assorted clips and fittings to the frame of the vehicle and to the gas tank. In these applications, the adhesive must stand up to elevated temperatures, UV light, moisture, salt water, solvents like motor oil and gasoline, and to high impact and vibration.
Henkel Corp.www.henkel.com
I use plasma in my lab and have seen a great improvement with bonding strength. I have never used corona or flame though.
We need to perform an adhesion of surfaces such polyethylene to polypropylene can you recommend a product that is suitable for the automotive industry.
Browse the most current issue of Design World and back issues in an easy to use high quality format. Clip, share and download with the leading design engineering magazine today.
Top global problem solving EE forum covering Microcontrollers, DSP, Networking, Analog and Digital Design, RF, Power Electronics, PCB Routing and much more
The Engineering Exchange is a global educational networking community for engineers. Connect, share, and learn today »
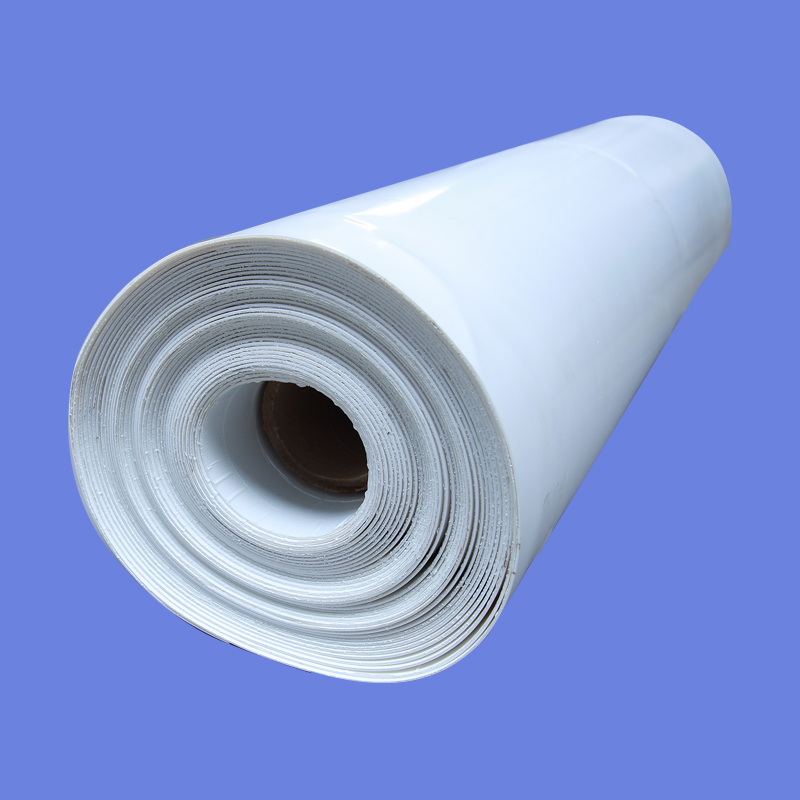
Walkway Board Copyright © 2023 WTWH Media LLC. All Rights Reserved. The material on this site may not be reproduced, distributed, transmitted, cached or otherwise used, except with the prior written permission of WTWH Media Privacy Policy | Advertising | About Us